BeWave and Inventory Automation: A Revolution in Hot Dog Management
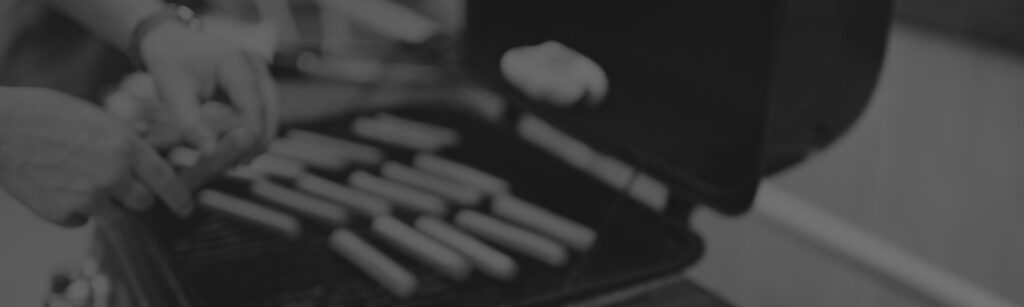
The Challenge: An Integrated Solution for Quality Meats
The BeWave Strategy: Understand, Integrate and Optimize
With warehouse operations at the heart of this project, it was agreed from the outset that the client would be responsible for sourcing the handheld barcode scanners needed to record all inventory movements in real time… or enough time to shout “all dressed “! For its part, BeWave would use its expertise to develop secure, robust mobile interfaces enabling any scanner to communicate directly with the company’s web service to manage data collection.
True to the philosophy that has forged its reputation, BeWave first made sure to question and fully understand the client’s reality, its existing systems and available R&D tools, while adapting to the level of knowledge of in-house teams who were well versed in the world of the Web. Above all, the aim was to accompany and facilitate the client’s journey throughout the implementation of this new system, and to adapt to their most precise needs, in a highly collaborative environment.
Mobile Interfaces for Greater Efficiency
Various options were presented to the customer to enable him to achieve his goal, particularly with regard to the choice of operating system (Android or Windows CE). BeWave also strongly suggested the use of an Open Source Web Application that could connect to Wi-Fi via a central server. In this way, all the devices would be linked together and could record information efficiently. As an added bonus, opting for this formula would make the choice of barcode readers much simpler.